THE PATTY WAGON
Story and photos by John Pellegrino
Our truck just pulled from the mud outside of Bozeman, Montana.
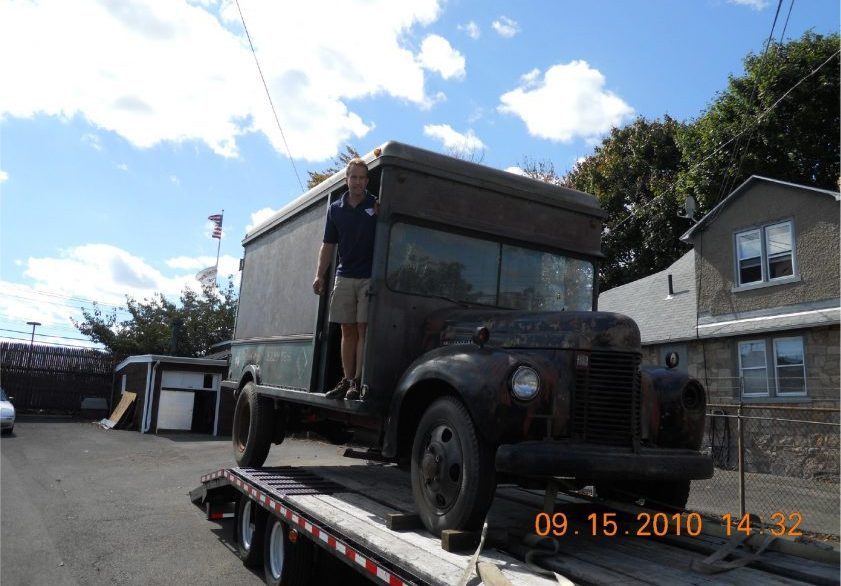
Lorin taking delivery of our truck on September 15, 2010.
Now that we had the truck, the search for someone to bring our vision to life would fall into the hands of an old Super Duper customer, Johnny Waz.
The fact that the under carriage of the truck was encased in Montana mud preserved all the mechanical and even the iconic IH red paint
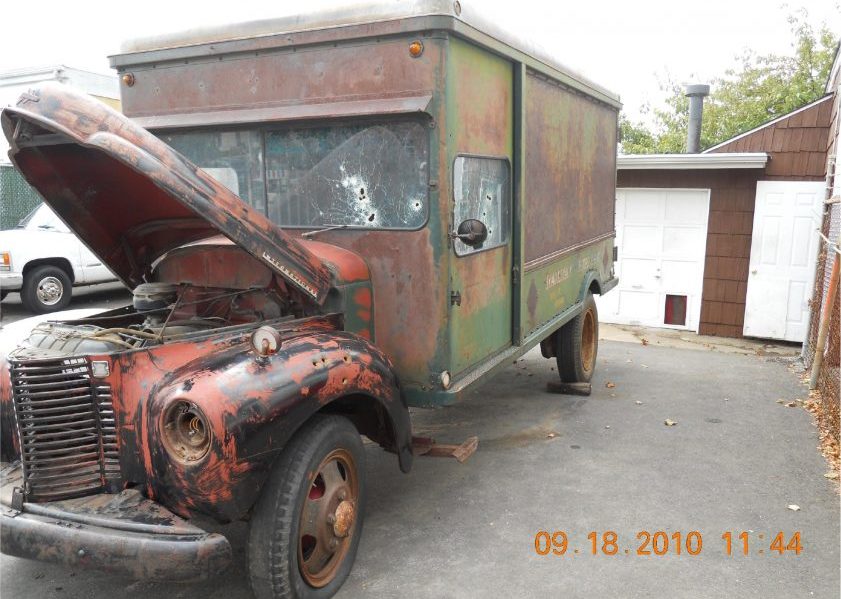
Other than a few bullet holes, some missing parts, and broken glass, this truck was in really good shape.
The entire truck is constructed with COR-TEN steel. This type of steel forms a layer of rust that protects the steel underneath from further deterioration. It is commonly used in statues and architectural features on buildings, as well as rail cars.
Even though it doesn’t look good from these pictures, things were not as bad as they appeared. All the parts in the cab were intact. They just needed some love.
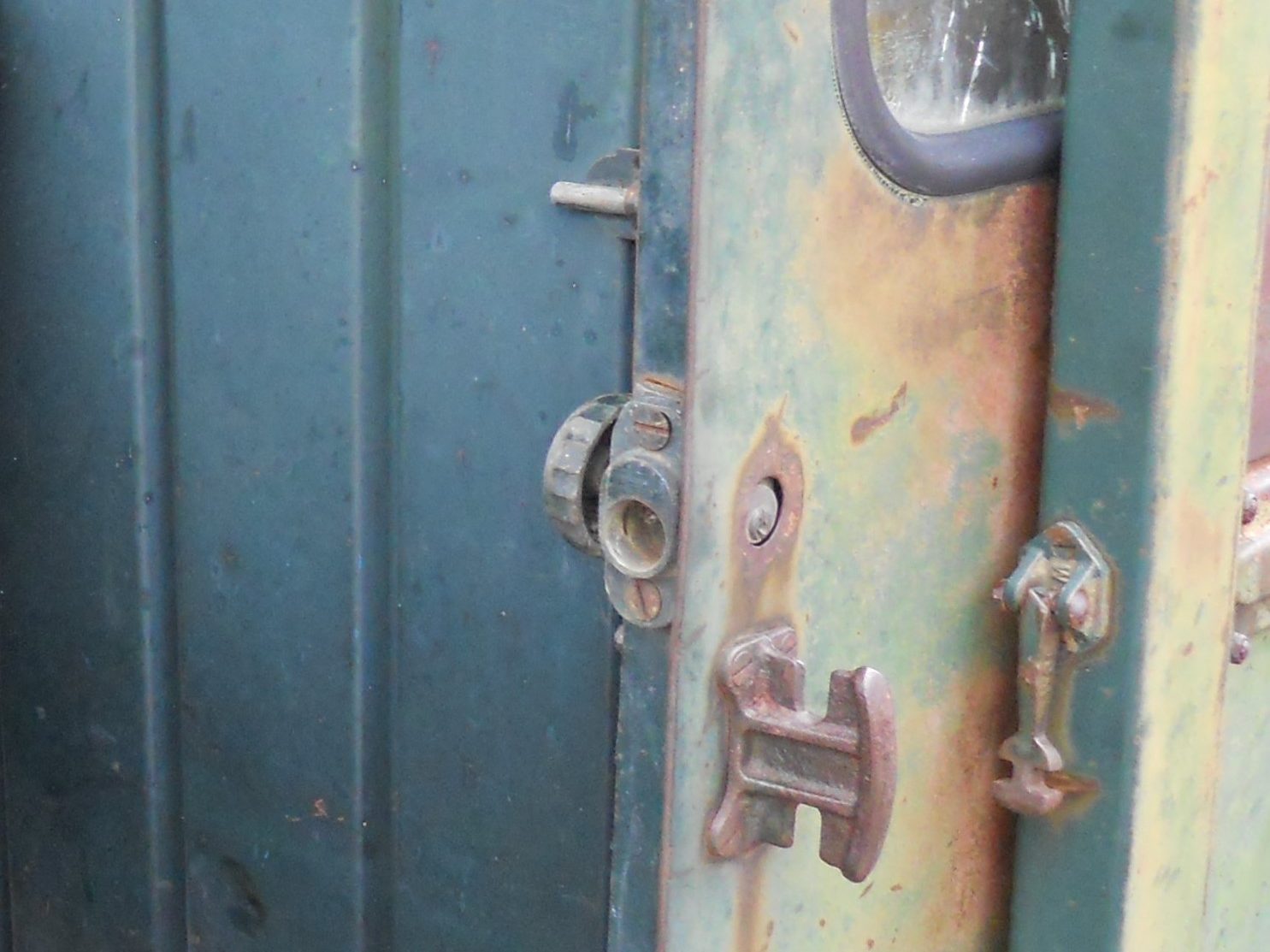
Even the original door latches were in perfect operating condition (Just no keys)
Lorin would eventually hand file operating keys for all the locks.
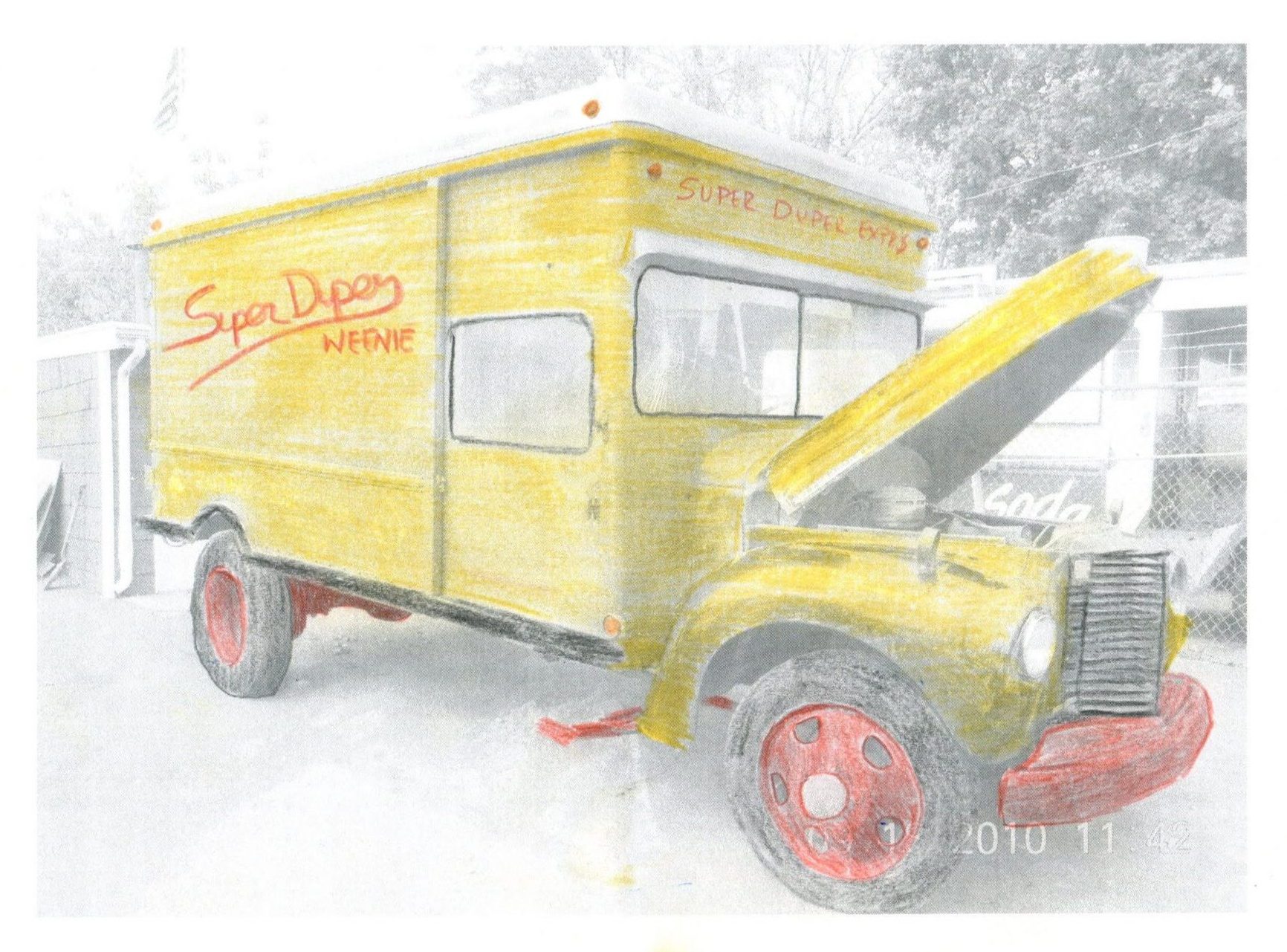
Now that the restoration had begun some big decisions had to be made about the color scheme. Pictured here is my first sketch of what I envisioned our truck would become. I definitely did not want to use the traditional Super Duper red, white & blue color scheme. I wanted something more period. Luckily the Wisconsin Historical Society keeps detailed records of everything International Harvester. Even the original paint codes. Yuma Cream No. 106 would be used for the body and Harvester Red No. 50 (of course) for the frame and rims.
The front fenders and grill of International Harvester K series trucks were designed and built to be fastened with only sixteen bolts. This allowed the entire front of the truck to be removed as one piece. As seen here, the entire front of the truck was removed and sent to our friend Milo Bertini of Trumbull to be sandblasted and prepared for paint. Notice the frame painted Harvester Red.
Amazingly, when the truck was delivered, all the original rims were piled in the back of the truck. These rims are what is called a Budd-style split ring rim. These rims were so dangerous to work with that they were discontinued from production. These along with their cousin the Split-Rim design earned the nickname “Widowmakers”. Only very qualified technicians will work with these rims. After having all six rims sandblasted and painted our friends at DeSantie Tire in Fairfield mounted the 1940 style Firestone tires.
Up to this point, the restoration went very smoothly.
These are a series of pictures of the truck after it was painted
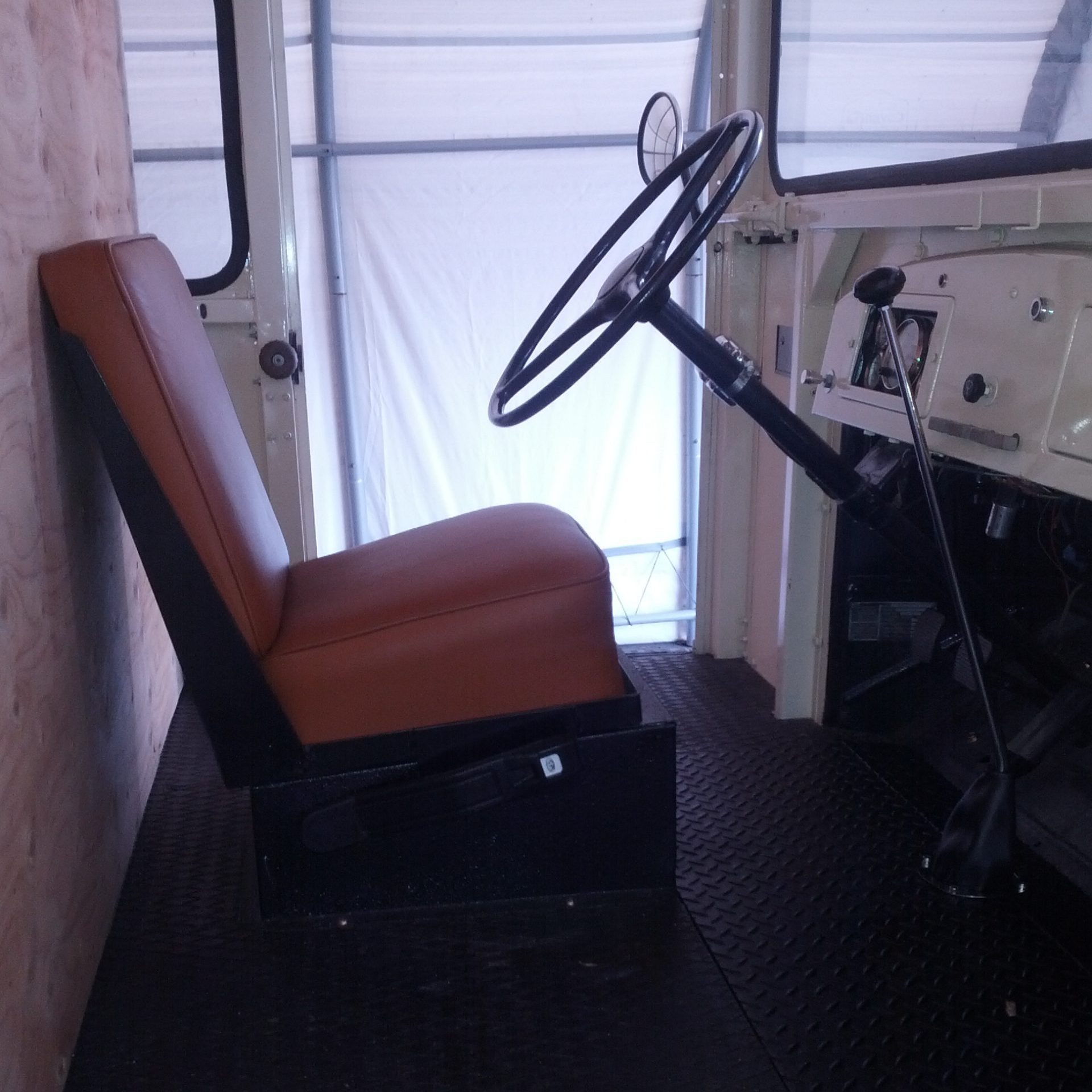
Wow! Doesn’t the cab look great from what we started with? Our friend Greg Franzino from Fairfield Auto Upholstery even made us a custom leather driver’s seat.
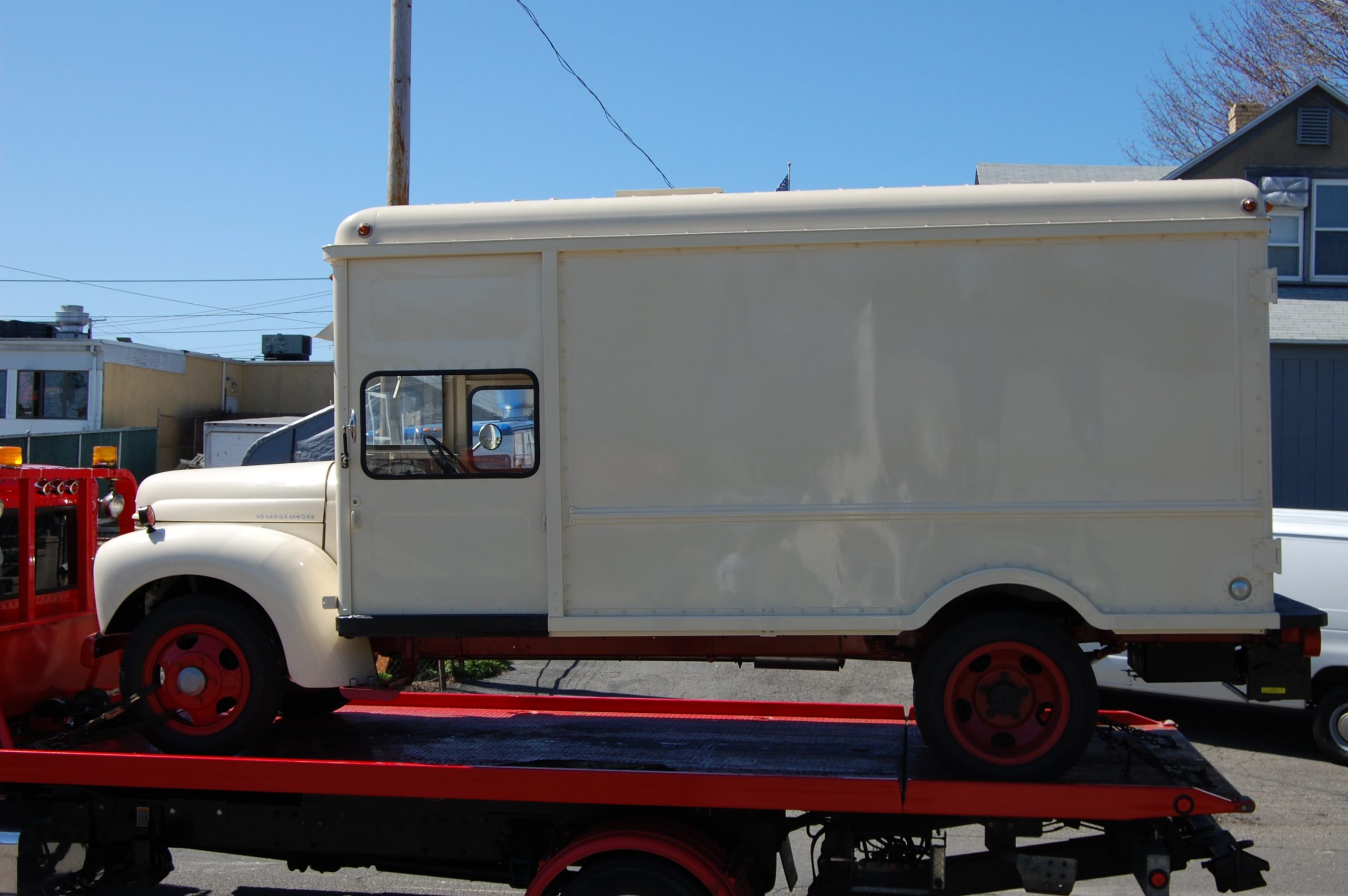
Well, that was easy. Haha! This is the part of the story where my brother and I would get an education in antique restoration. This would be a ten-year journey to get our truck to the point where we could depend on it to travel at least up to an hour away from Fairfield (without breaking down). That would be easier said than done. For awhile our truck would spend more time on a flatbed being towed in rather than on the road.
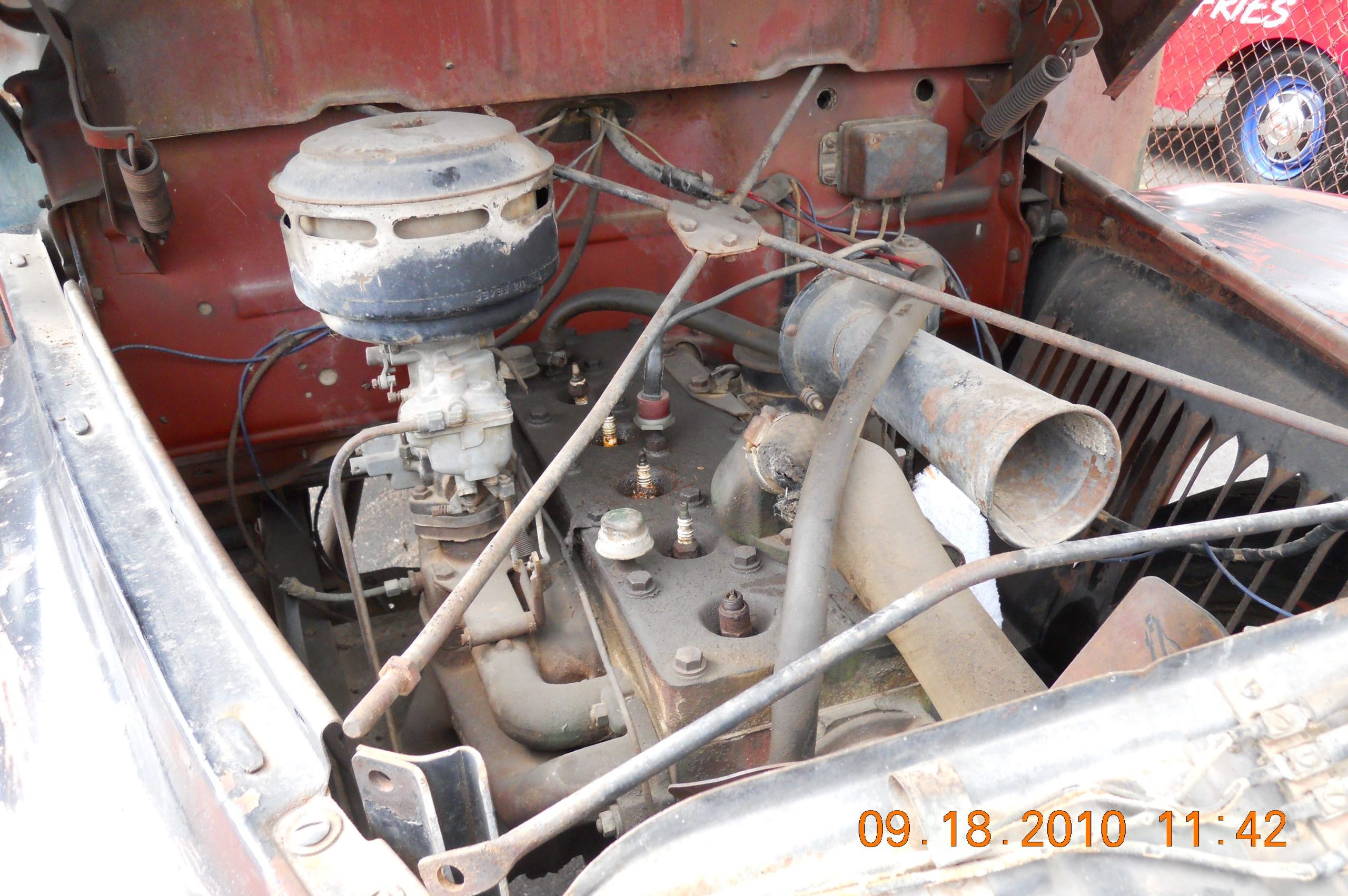
What we needed to accomplish was to take the old motor and transmission out and replace it with a modern one. Pictured here is the original motor, a Green Diamond 214 flathead 6 cylinder, and it would produce a top speed of about 25 mph. Not looking to break any speed records, we did need to at least keep up with traffic.
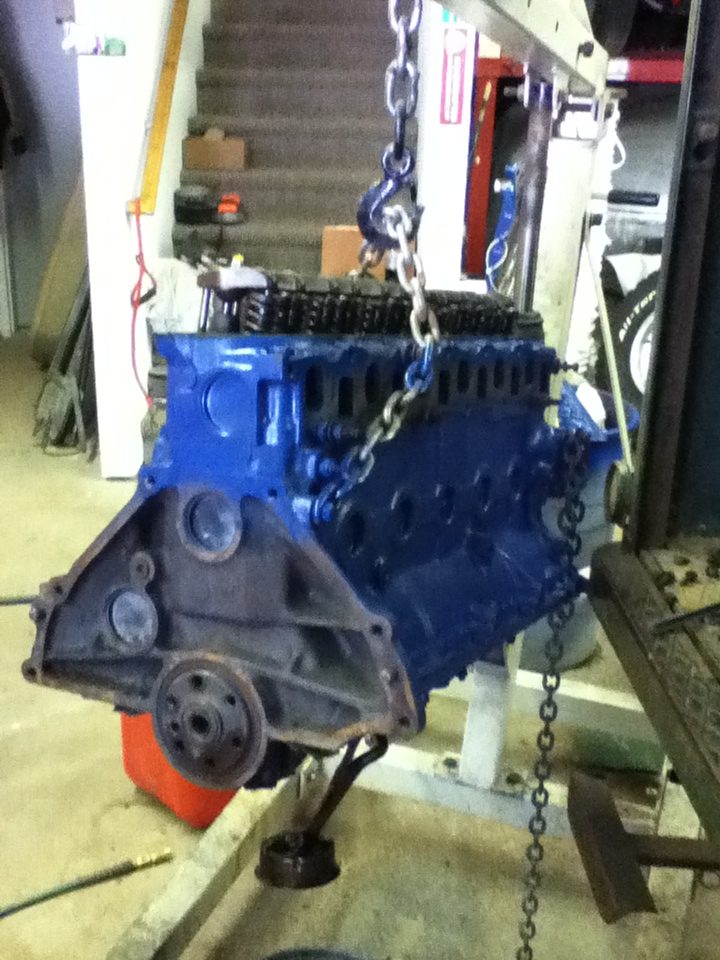
Our first go at this did not go well. We located the motor that would fit in the truck a Ford 300 straight-six. We would have it completely restored and installed in the truck. On its maiden voyage out of the garage, the engine would seize on Route 8. The shop did a wonderful job on the exterior and interior of the truck, but come to find out they were in way over their head on the mechanicals of the restoration.
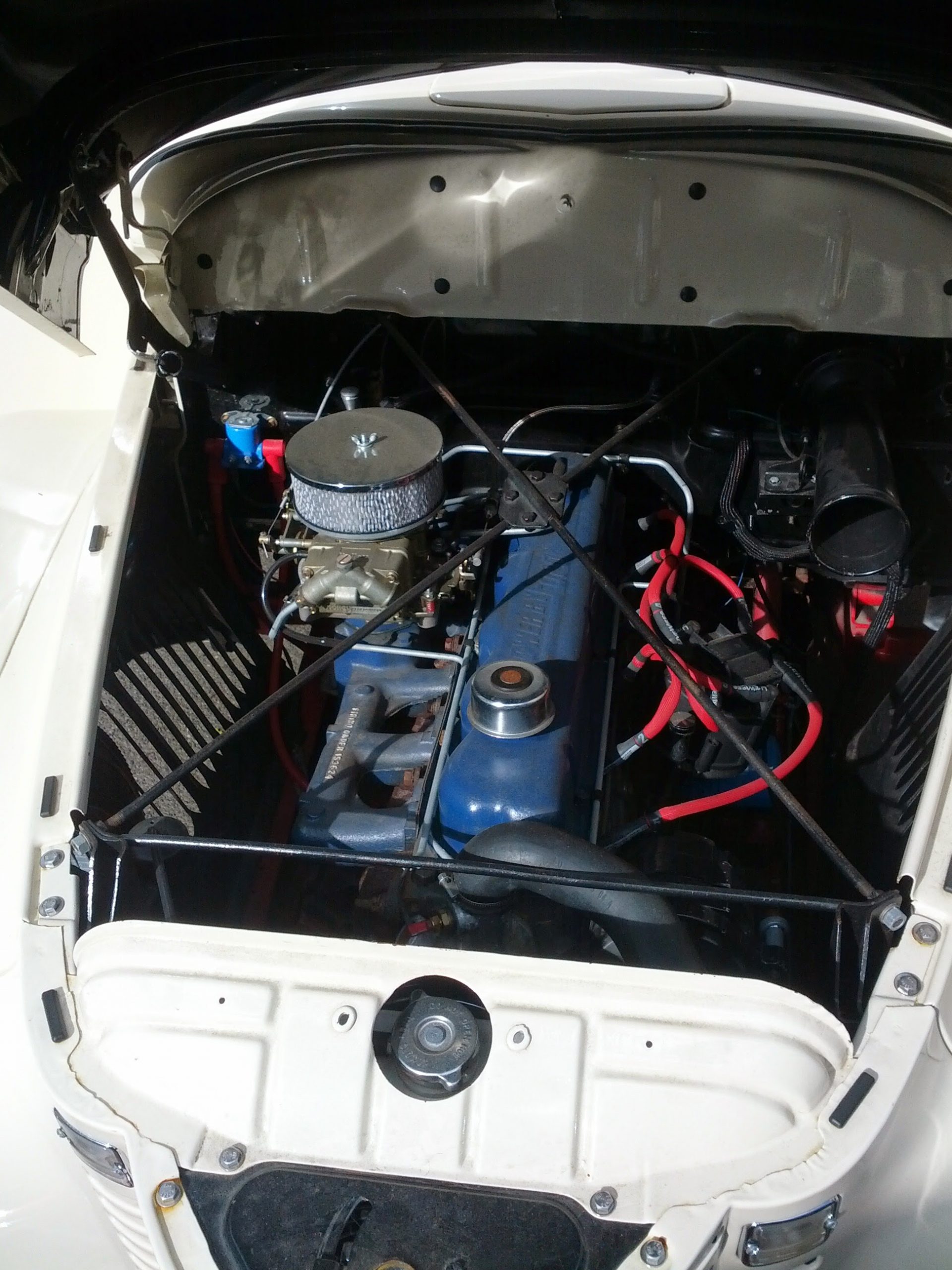
Somewhat disappointed and having a little crisis of confidence, we knew we had to pull it together to find the right people to do the job. We just invested a good sum of money and have nothing to show for it.
Our dad loved old trucks and he and his friends would restore Ford Model A’s back in the 1970s & 80s. My brother and I as young boys would love to hang around the garage and watch. These connections would lead us to Jerry and his son Greg. This father and son team would immediately identify everything that was done wrong and within a year would deliver to us a fully operating truck.
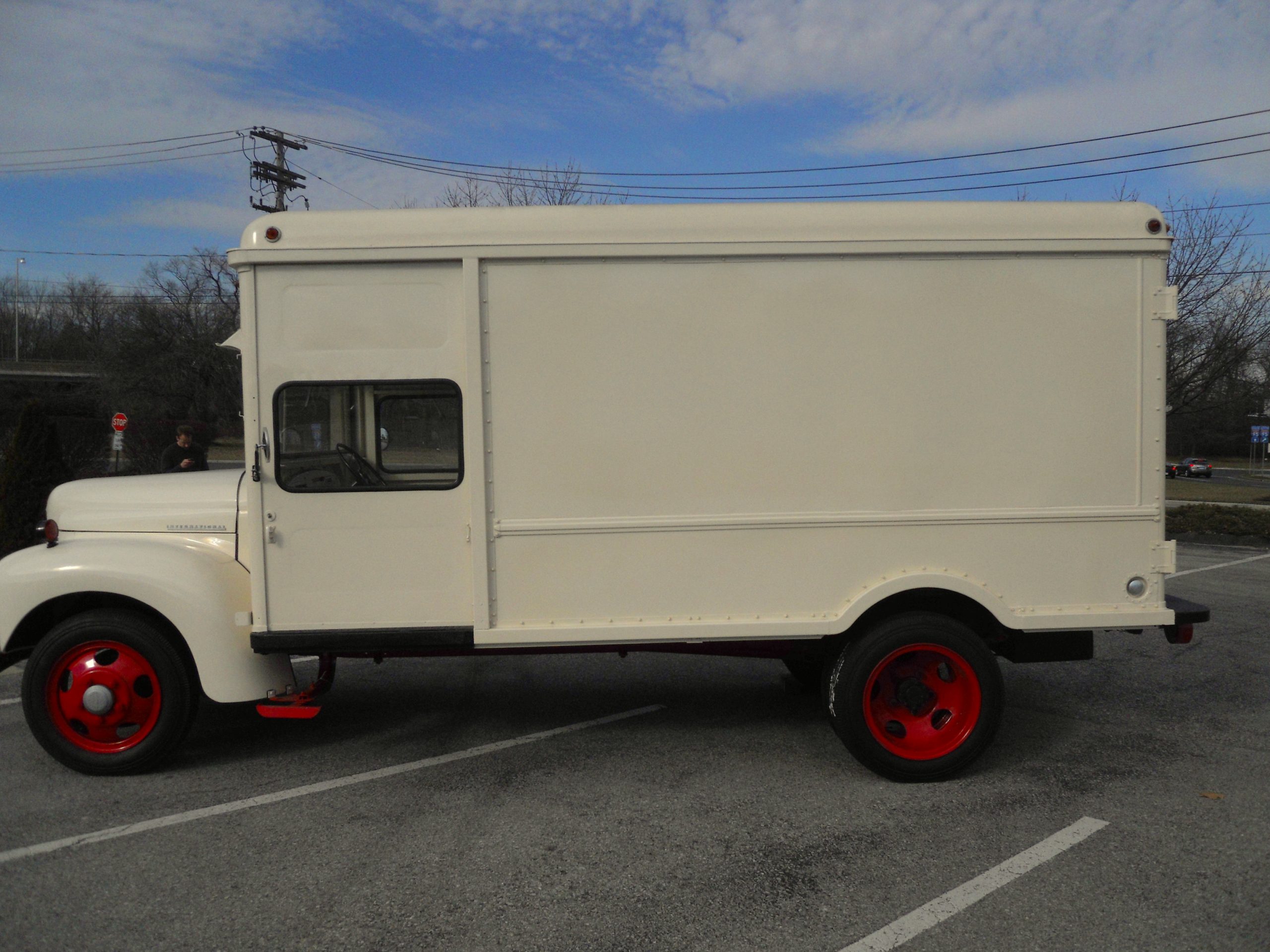
So you would think at this point we have a happy ending to our story. Not quite. Over the next few years, we would have to be towed in many more times. Everything mechanical on this truck was either an original part that was restored or a custom-made replica. There was no manual for blending old parts with new parts. It was years of trial and error. Reconstructing the brake system, redesigning the cooling system a number of times to prevent overheating, stabilizing the front end to prevent “death wobbles”, and installing not one but three different transmissions. But after all that, I think we finally got it right!
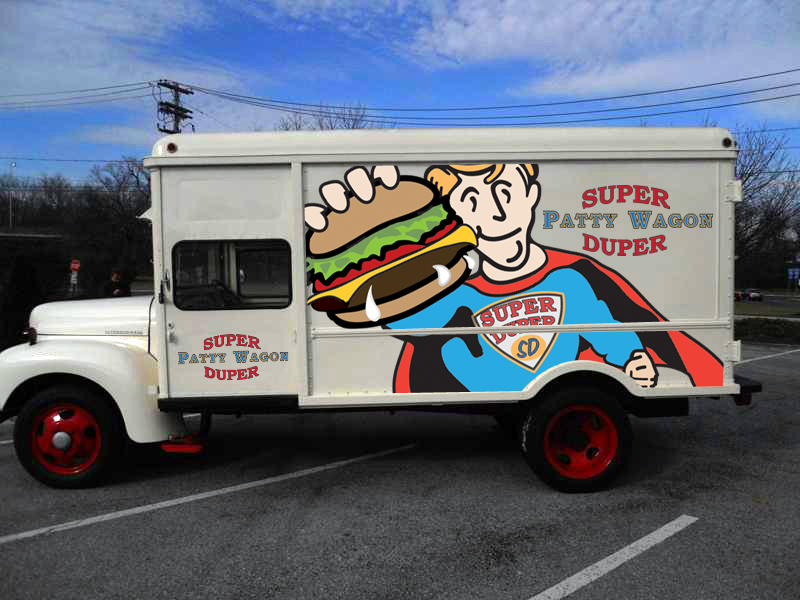
The next phase was fun. My idea was to bring the Super Duper brand back in time. I definitely knew I wanted to use the style of the original REA lettering on the truck. After that, I was not sure, but I did know who to call. Randy Garbin has long been part of the Super Duper family and is responsible for most of the graphic representations of our brand. He immediately told me what he wants to do. Draw the Super Duper guy as if he was conceived in the 1940s. And just like that, we had our graphics for the truck.
This picture is the first rendition sent to me. I would slightly change over time, but you can miss the big Super Duper guy coming out at you.
So what about the kitchen?
As with everything else on this project we had to custom fit a kitchen into a smaller space than we are accustomed to. With the help of our friends, Jeff and Jody from General Sheet Metal in Bridgeport we collaborated to design and build a custom-made kitchen for our truck. Notice the low profile hood vent. Jeff and Jody cut and welded the vent directly into the contours of the truck.
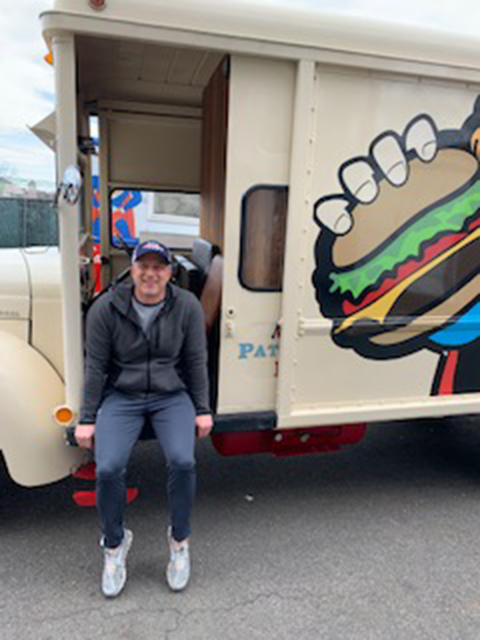
Picture of John and his truck.

It has been a long and trying experience, but so worth it. The project definitely took longer than we anticipated, but in the end, we built that “one-of-a-kind food truck” we initially envisioned years ago.